Yachts
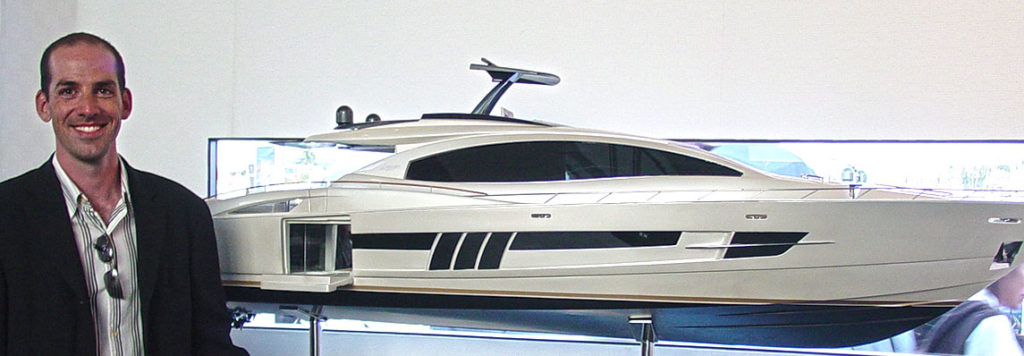
Forse la parte più sorprendente di come sono entrato in questo settore è che non avevo alcun background in esso per cominciare. Come per tutti i miei interessi, una volta scoperto un nuovo argomento che ha catturato la mia attenzione, l’avrei studiato a fondo, ne avrei compreso la storia, i metodi di costruzione, i materiali, l’evoluzione nel settore… ma con l’industria navale non avevo un tale contesto.
Mi è stato presentato un ingegnere nautico che mi ha invitato a visitare il cantiere e ho accettato per cortesia piuttosto che per interesse. Il mio abbigliamento informale era considerato formale su un molo Floridiano; per cio, quando mi è stato presentato al titolare, ha pensato che fossi venuto per un colloquio e, visionario che lo fosse, in pochi minuti e alcune domande mirate ha scoperto che eravamo come due gocce d’acqua.
In particolare, gli piaceva il fatto che conoscessi molti mestieri, che fossi creativo e che non avessi alcun vincolo in mente sul “così lo abbiamo sempre fatto”. Ho pensato spesso a questa intervista in seguito e mi sono reso conto che con queste poche domande ben scelte, ha imparato che ero versatile, un risolutore dedicato di problemi, un studente appassionato, flessibile, collaborativo, di mentalità aperta, innovativo e che pensavo fuori dagli schemi. Ovviamente non avevo portato il mio curriculum, ma dalla nostra conversazione ha scoperto che avevo un background in affari, avevo studiato scienze dei materiali e ingegneria e parlavo diverse lingue.
Per assicurarsi che la sua intuizione fosse giusta, ha suggerito di incontrarci di nuovo qualche giorno dopo e di portare con me alcuni schizzi di yacht, i miei primi. L’unica cosa che non poteva sapere subito era il mio senso estetico. La seconda volta che ci siamo incontrati, non ero in grado di parlare perché mi erano appena state rimosse le tonsille e tutta la comunicazione avveniva attraverso lo schizzo, quindi ha visto che non ero limitato ai rendering al computer che può richiedere giorni, ma potevo davvero disegnare davanti di un cliente per mostrare la mia visione o chiarire la loro in un istante. Forse ciò che ha concluso l’accordo è stato quando ha preso tre dei cinque schizzi che avevo realizzato e mi ha mostrato i suoi da un brainstorming che aveva avuto poche settimane prima: erano straordinariamente simili.
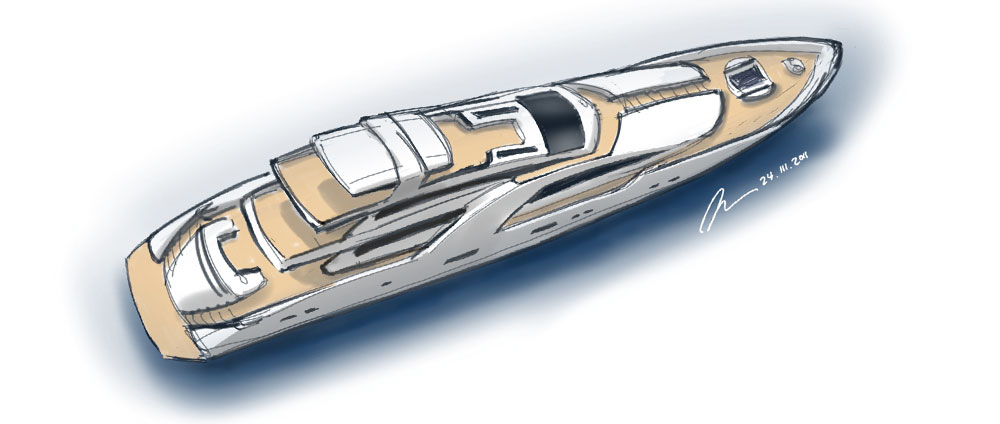
I miei primi due giorni di lavoro li ho passati imparando a usare Rhino 3D che non conoscevo. Mi sono proposto la sfida di progettare una barca a vela su un mare agitato, con le vele completamente spinte dal vento, e in due giorni, dopo tentativi ed errori, ci sono riuscito e ho saputo usare il programma. Questo era un settore di cui non sapevo nulla, a parte le competenze trasferibili e ciò che avevo imparato sul design, su altri modi di trasporto o sulla biologia. Era essenziale che imparassi velocemente, e senza limitarmi alle modalità di costruzione tradizionali.
La prima scrivania che mi è stata data era accanto a quella di un architetto navale e gli ho spiegato come per ogni mio progetto tengo conto della produzione. Abbiamo avuto una buona conversazione ed è stato davvero onesto con me dicendo “Ci crederò quando lo vedrò!” – Ho sorriso perché sapevo che avrebbe cambiato idea rapidamente, e infatti lo ha fatto. Non ho una laurea in ingegneria, ma al di là dei miei studi e ricerche, ho interagito abbastanza con ingegneri di vari settori per capire cosa dicono senza che me lo debbano tradurre. È essenziale che interagiamo in modo significativo perché sento che il mio lavoro è complementare al loro.
Per imparare il più possibile, il più velocemente possibile, ho ricercato, ascoltato, fatto domande, osservato la produzione. Ho iniziato a interagire coloro che avevano lavorato il più lungo nel settore, chiedendo loro come erano state fatte le cose, offrendo alcuni suggerimenti, soprattutto assicurandomi che capissero che il mio obiettivo era lavorare in simbiosi con loro per rendere più facile il loro lavoro, e anche semplificare i loro metodi di produzione. In effetti, erano stati abbastanza sinceri con me, spiegando che la loro esperienza di designer era qualcuno che gli presentava un progetto e che in qualche modo dovevano realizzarlo. Spesso non si è pensato alla complessità che avrebbe potuto portare alla produzione.
Così, quando avevo un progetto da presentare loro, avevo una regola: non potevano darmi un “no” assoluto, ma piuttosto un “no, perché”. Se non era possibile per loro costruirlo come l’avevo progettato io, ho chiesto loro di spiegare perché pensavano che fosse così. Con questa interazione ho imparato a conoscere i loro metodi di costruzione e se ci fossero state delle inefficienze che avevano dovuto affrontare per anni, potrei anche risolverle.
In definitiva, questo ha creato un forte legame e un rapporto di fiducia e rispetto reciproco. Quando qualcosa sembrava non funzionare nella realizzazione dei miei disegni, venivano direttamente da me per risolverlo, risparmiando tempo prezioso. Entro un anno dall’inizio, sono diventato noto come colui che ha risolto problemi apparentemente insolubili, spesso sull’ottimizzazione dello spazio, e tutti in azienda sono venuti da me.
Circa una settimana dopo aver iniziato, il primo progetto di cui ero responsabile è stato l’intero livello del flybridge di uno yacht da 35 metri. Fino ad allora il flybridge era sempre stato aperto e il cliente lo voleva chiuso e più spazioso. La sfida consisteva nell’integrare strutturalmente e visivamente un flybridge più grande e completamente chiuso al resto del yacht. Abbiamo eseguito una scansione 3D dello yacht a ponte aperto esistente, un processo che all’epoca era praticamente sconosciuto. Con questo come base, ho progettato la nuova versione del flybridge, assicurando un’integrazione fluida tra i livelli superiore e inferiore e un design che scorreva con il resto dello yacht. Il cliente, che era un dignitario straniero di altissimo rango, e aveva intenzione di utilizzare lo yacht come yacht da conferenza, è stato soddisfatto del risultato.
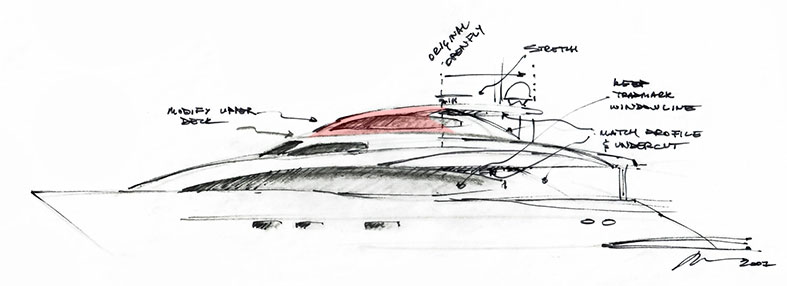
Dopo questa prima realizzazione di successo, mi è stato assegnato il compito di lavorare alla progettazione e produzione di diversi yacht in costruzione, risolvere problemi su più progetti simultanei, imparare, e rafforzare il mio legame con il resto del team, è stato molto stimolante e m’è piaciuto molto.
Nel giro di pochi mesi abbiamo iniziato un progetto epico: se potessimo progettare tutto ciò che volevamo, e se non ci fosse limite a ciò che potevamo aggiungere a uno yacht, quali sarebbero le caratteristiche più “cool” che vorremmo implementare?
Era gennaio 2008 e ricordo ancora la sessione di brainstorming, perché è diventata una delle più grandi avventure della mia vita professionale.
Ci siamo scambiati idee innovative e, con la visione e il coraggio del titolare della ditta, abbiamo ricevuto la via libera per realizzarle per lo yacht finale. È stato emozionante far parte della squadra per realizzarli. Sapevamo già che volevamo presentarlo al Fort Lauderdale Boat Show di quell’anno a novembre. Progettare e costruire uno yacht rivoluzionario in meno di un anno? È stata una tale sfida che Yachts International ha pubblicato un articolo esclusivo in 3 parte seguendo l’intera costruzione.
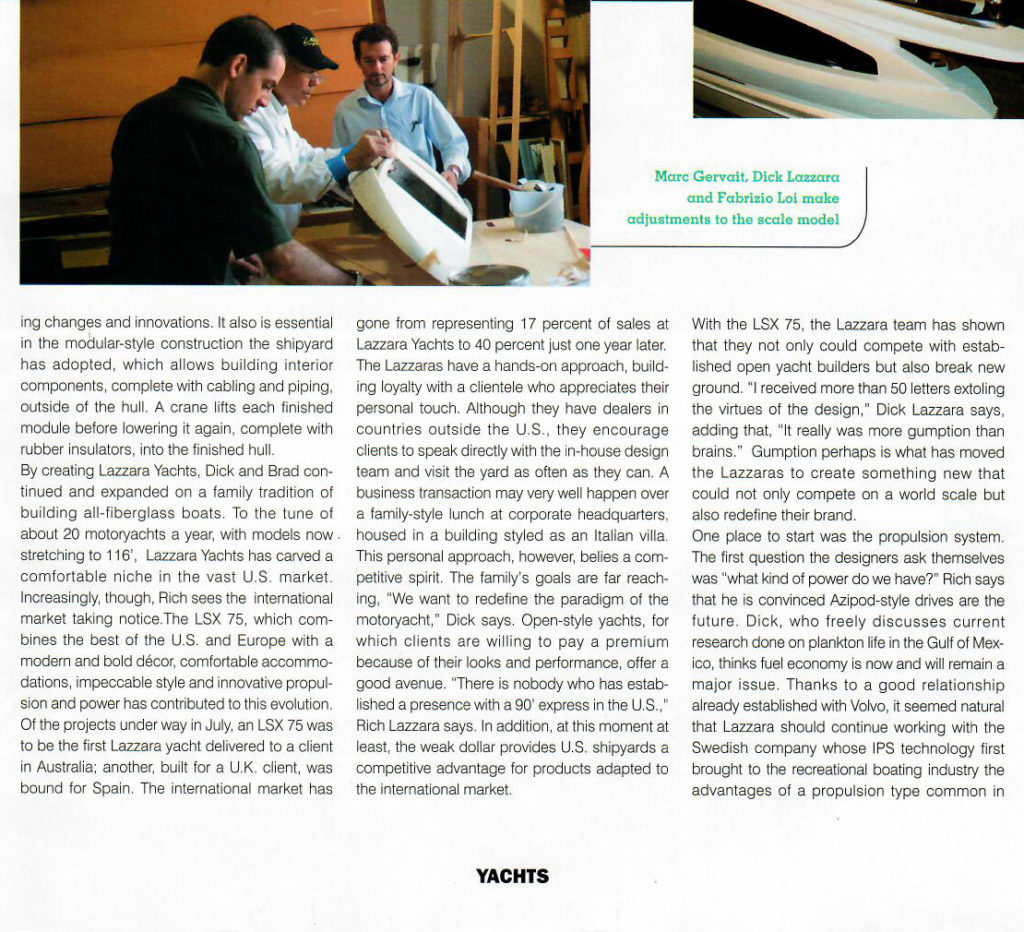
Il processo di progettazione ha coinvolto quattro di noi nella realizzazione di schizzi, per poi passare a un modello multimediale. Le proporzioni della barca prendevano letteralmente forma mentre sovrapponevamo pezzi di nastro adesivo nero sulla fiancata per decidere, ad esempio, i contorni delle finestre. Gli yacht di questa azienda avevano linee di finestra inconfondibili e dovevamo trovare un modo per mantenere riconoscibile il marchio. Trovavamo la nostra ispirazione ovunque, anche nell’industria automobilistica, ad esempio per la forma dello scafo. Ognuno di noi ha aggiunto linee, modificato la forma fino a quando non siamo stati tutti d’accordo sulle proporzioni generali dello yacht. Avevamo iniziato a progettare lo yacht pensando che sarebbe stato un yacht lungo di 27 metri ma la forma si è affusolata, è diventato lungo di 28 metri.
Una volta soddisfatti del look, l’ho scansionato, inserito nel computer e modellato in 3D, rifinendo tutte le superfici, mantenendo le proporzioni di ciò che avevamo scolpito nel multimediale e rendendolo simmetrico. Quindi abbiamo scolpito un modello con la fresatrice in una schiuma ad alta densità, l’abbiamo dipinto con un primer per dargli un guscio duro, e abbiamo ripetuto lo stesso processo modificandolo con argilla, legno, raffinandolo fino a quando non ci è piaciuto a tutti. Abbiamo affrontato questo processo tre volte finché non siamo stati tutti sicuri e abbiamo concordato che questa fosse la forma giusta. Infine, abbiamo fatto ritagliare un modello 3D fatto di materiale molto denso da un’azienda specializzata, che ha permesso l’inizio del marketing.
A questo punto, era chiaro che ero il migliore per realizzare superfici finali di classe A, quindi è stato assegnato a me di farle. I metodi di costruzione nel settore degli yacht differiscono da qualsiasi altro settore. Ricordo che al Cleveland Institute of Art and Design dovevamo presentare ogni nostro progetto in “forma esplosa”. Quell’esercizio è stato un’ottima preparazione per progettare lo scafo degli yacht in uno stampo. Le compagnie di yacht spesso realizzavano i propri scafi con stampi in un unico pezzo con rilascio verticale, ma questa azienda utilizzava uno stampo a rilascio diviso laterale.
Ne consegue che se non è perfettamente disegnata, se c’è una sola superficie, per quanto piccola, che non è angolata in modo corretto e preciso, lo stampo non si staccherà. Un’ulteriore complessità è che lo stampo era modulare e, sebbene ciò aggiungesse flessibilità, era importante poter visualizzare mentalmente tutte le parte prima di utilizzare il software del computer per progettarlo. Il computer è uno strumento e può solo rendere ciò che hai visualizzato nella tua mente.
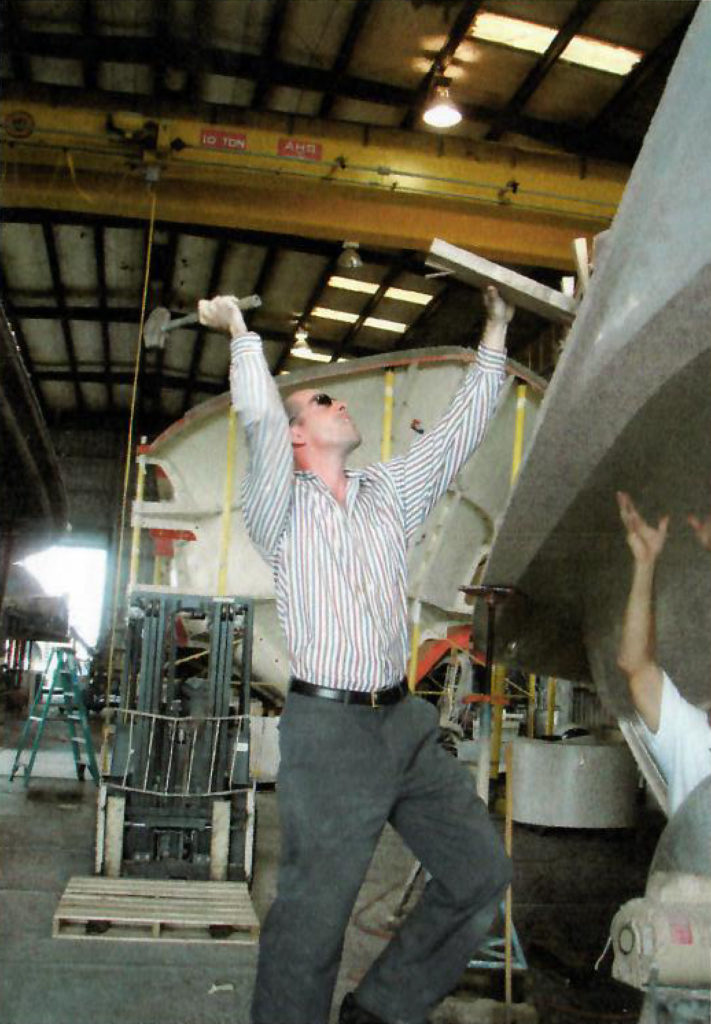
Anche i motori furono i primi al mondo. Volvo aveva costruito 4 motori prototipi mesi prima che entrassero completamente in produzione. Stavamo per incorporare questi motori nel nostro yacht e presentarli. C’era una partnership preesistente con Volvo e la nostra azienda, e prima che mi unissi a loro aveva vinto il premio più innovativo a Cannes per aver progettato lo scafo del loro yacht da 23 metri per abbinare e ottimizzare la propulsione. All’epoca eravamo gli unici al mondo ad aver creato la forma dello scafo per il pacchetto motore e trasmissione.
Progettare ogni superficie di uno scafo di 28 metri è molto più che “far esplodere” e “allungare” una scansione 3D di uno scafo di 23 metri, ci sono molte sottigliezze. Inoltre, è stata la prima barca al mondo ad avere questo sistemo di propulsione. 4 motori potrebbe sembrare un aumento dei consumi, ma erano molto efficienti e in effetti dimezzavano quasi il consumo di carburante, che era molto significativo e senza precedenti all’epoca.
Fin dall’inizio avevamo deciso le varie fasi del progetto per ottimizzare la produzione. La prima cosa che dovevo fare, prima ancora di pensare agli interni, era lo scafo, senza il quale non si può costruire nulla. Ho fatto tutte le superficie per lo yacht e dove sarebbero andate le finestre. Una volta fatto, ho potuto inviarlo a qualcuno che si occupi di fare il modello su piccola scala. Successivamente ho dovuto modificare nuovamente ogni singola superficie per tener conto della produzione attuale. Niente da dimenticare: angoli di sformo per poterlo estrarre dallo stampo, e ovviamente tutto ciò che ha a che fare con l’idrodinamica, compreso e ottimizzando le prestazioni dei motori. Con tutta la precisione che comporta e senza il diritto di commettere un solo errore. Stavo lavorando uno a uno con il presidente che aveva sviluppato un’abilità istintiva nel corso della sua carriera da poter guardare un progetto e sapere se era necessario cambiare una leggera angolazione per l’idrodinamica. Questa interazione diretta e il dialogo mi hanno permesso di imparare molto da lui e mi hanno dato l’opportunità di introdurre nuovi metodi di “streamline” la produzione.
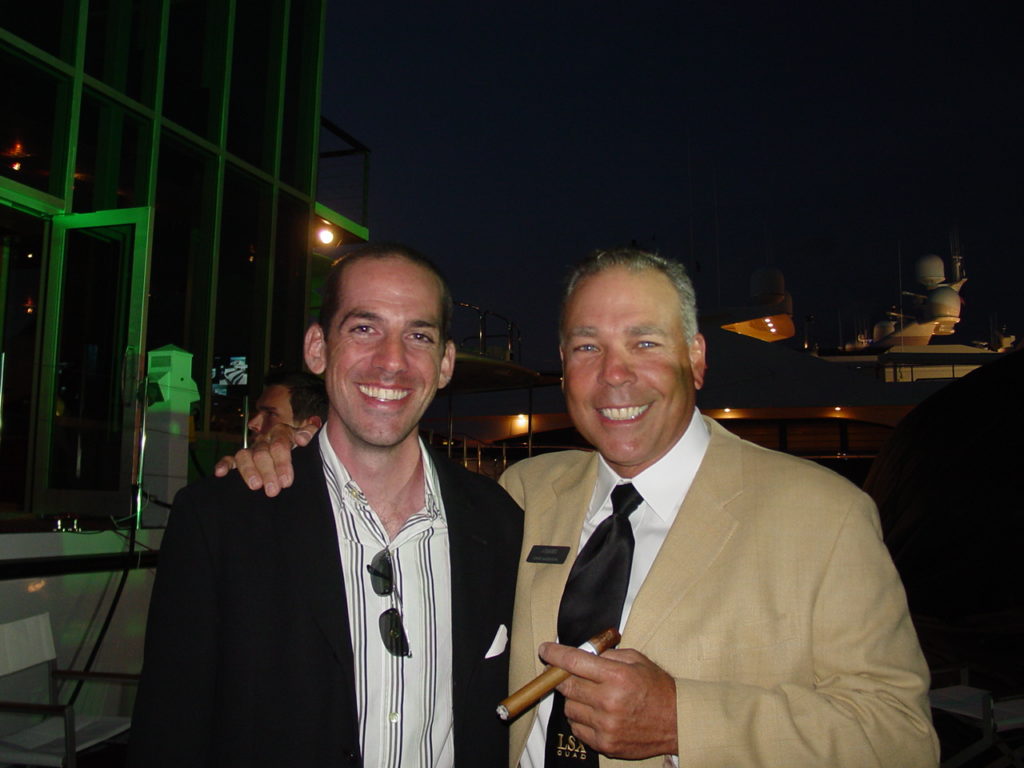
Conoscevo i contorni dei pezzi che sarebbero arrivati dopo (come quegli per attaccare il ponte allo scafo) e come volevo che fossero collegati, quindi potevo già inoltrare quelle informazioni a un’azienda per ritagliare un stampo maschio per il scafo finito, che avremmo ricevuto diverse settimane dopo, e dal quale avremmo potuto creare lo stampo di produzione. Detto questo, questi pezzi non erano ancora stati progettati e quindi abbiamo dovuto lavorarci su in parallelo. Una volta conosciuta la forma finale dello scafo, abbiamo potuto iniziare a creare gli interni. Mentre stavamo facendo gli interni, abbiamo potuto lavorare sulla progettazione del ponte per adattarsi allo scafo in arrivo e, nel frattempo, ho potuto lavorare sulla progettazione di tutti gli inserti dello stampo dello scafo.
Stavamo pensando di aggiungere un tender e una moto d’acqua nel garage di poppa e l’avevamo già pubblicato sul nostro marketing e nella stampa, ma non l’avevamo ancora progettato ed io ero interamente responsabile della aft beach (spiaggia di poppa). Ho progettato il pavimento del garage di poppa in modo che potesse essere sia rialzato per essere allo stesso livello della spiaggia di poppa, sia abbassato per ospitare il tender e la moto d’acqua. In quello posto in assenza di tender e moto d’acqua avevo progettato lo spazio per uno schermo gigante, un impianto audio, luci, pronto a trasformarsi in una spiaggia da festa. Dato che era proprio sopra i quattro motori e le trasmissioni, l’ottimizzazione dello spazio era assolutamente fondamentale. Fondamentale era anche poterli accedere facilmente per il servizio, particolarmente dentro e fuori senza compromettere la struttura.
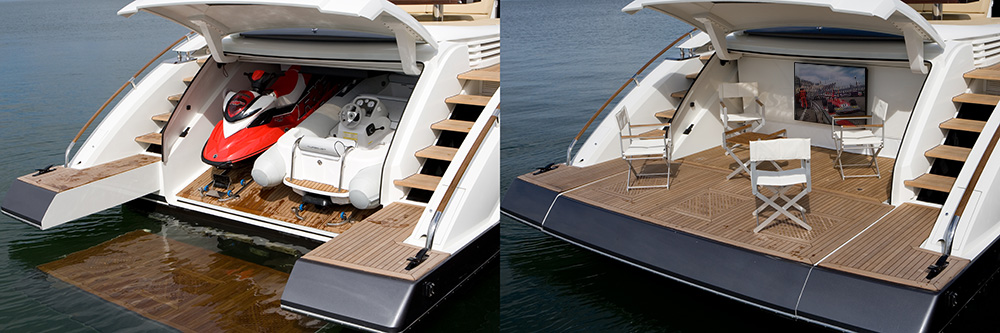
Quando la squadra di Volvo è arrivata con i suoi 4 prototipi di motori, sono stato io a supervisionare il processo di installazione nello yacht, e gli ho spiegato come installare i motori e in quale ordine. Era stretto, ma ha funzionato!
Una volta che avevo disegnato lo spazio per i motori, ho potuto disegnare tutti gli allestimenti interni per ogni stanza, bagno e doccia. Le forme non erano ordinare, mi sono assicurato di massimizzare l’uso dello spazio e di ottimizzare la funzione, con un ambiente estetico.
Per il primo articolo, avevamo realizzato un rendering che prevedeva un balcone laterale. La domanda che era nella mente di tutti era: dove metteranno i motori? Di solito, i motori dovrebbero essere esattamente dove viene mostrato il balcone laterale! Piu precisamente, i motori tradizionali avrebbero dovuto essere collocati dove avevamo posizionato la vasca idromassaggio per luminoterapia della Master Suite, che aveva una vista diretta sul balcone… ma non si trattava di motori tradizionali. Il sistema Volvo non aveva un albero perché erano isopodi, quindi con i pod (timone ed eliche in un’unica unità) posizionati proprio sotto la trasmissione, che era direttamente collegata al motore, potevamo posizionarli più indietro.
Questo è stato un operazione complessa: era molto di più che creare un bel balcone. Dopo aver deciso di realizzare un balcone laterale, abbiamo deciso che dovrebbe essere a rotazione e, naturalmente, per motivi di sicurezza, dovevamo avere diverse fasi di guasto. La sicurezza era la priorità assoluta. Oltre a trovare l’asse di rotazione, mi è stato assegnato il compito di come adattare il balcone al lato della barca in posizione chiusa. Per rientrare nella nostra ristretta timeline, dal momento che dovevamo finire prima di tutto il progetto dello scafo, ho dovuto risolvere velocemente la domanda delle dimensioni esatte del balcone, o la taglia del “buco” temporaneo sul lato dello scafo.
A questo punto, non avevamo idea di quale meccanismo useremmo. Avevamo un buco all’interno dello scafo, ma non abbiamo ancora idea di come far muovere la piattaforma corrispondente, conoscendo solo il loco dell’asse di rotazione. Un balcone del genere su uno yacht di queste dimensioni, così vicino all’acqua (1 metro sopra il livello dell’acqua), non era mai stato nemmeno tentato prima. Abbiamo contattato diverse aziende a livello internazionale e tutte hanno risposto con vari livelli di diplomazia che eravamo fuori di testa e che non volevano avere nulla a che fare con questo.
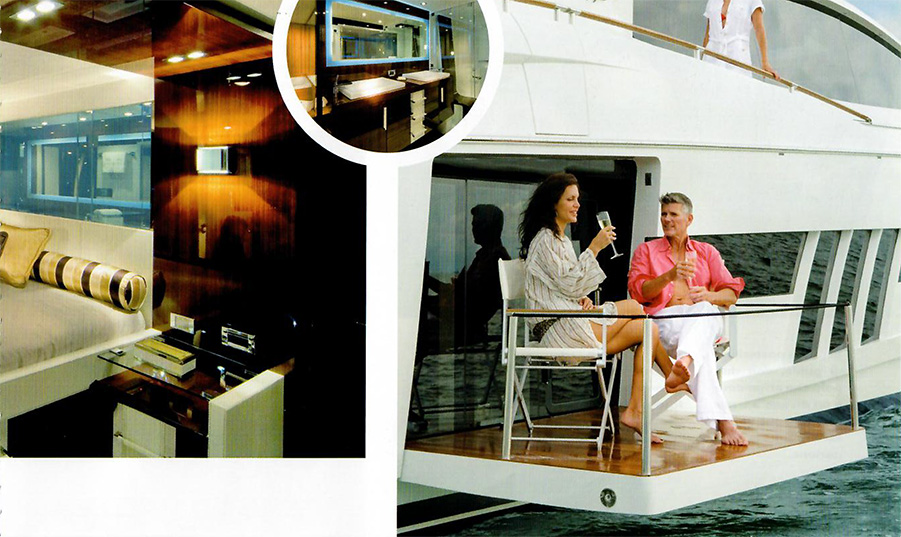
Ho passato ogni sera dopo il lavoro per tre settimane con il capo della ditta e l’ingegnere principale, e abbiamo discusso insieme su come farlo funzionare in sicurezza. Ci stavamo tutti scambiando idee e, una volta concordato il meccanismo e sentito che avrebbe prodotto il risultato che ci aspettavamo fornendo al contempo sicurezza assoluta ai nostri clienti, ho iniziato a progettarlo. Avevamo parecchi meccanismi di sicurezza per proteggere l’integrità dello scafo, l’ultima istanza era che il balcone poteva essere strappato senza alcuna infiltrazione d’acqua.
Questa è stata una parte particolarmente importante e delicata della costruzione. Volevo essere certo che fosse fatto correttamente e mi sono reso conto che ci sarebbe voluto troppo del prezioso poco tempo che avevamo per spiegare esattamente cosa stavo cercando. Così, ho realizzato io stesso sia il pavimento in teak del balcone che il meccanismo di chiusura, insieme all’artigiano a cui era stato assegnato il compito. Fu allora che mi guadagnai il pieno rispetto degli artigiani che stavano costruendo lo yacht. L’avevo progettato e costruito, e non avevo paura di sporcarmi le mani per costruire la mia visione: questo ha creato un legame innegabile, perché il team di produzione mi ha visto da quel momento in poi come uno di loro.
Ho iniziato a lavorare sul sistema di ancoraggio, ma mi è stato detto che era troppo complesso e che l’avrebbero dato a specialisti con cui avevano lavorato. In effetti, eravamo a corto di tempo e hanno pensato che sarebbe stato meglio delegare questa parte del progetto. Pertanto, il primo 92′ (28 metri) include il sistema di ancoraggio specializzato. Era molto costoso e complesso da installare. Una volta terminato il prototipo, con un po’ più di tempo, sono stato in grado di progettarlo da solo, con la stessa qualità e costava un terzo dell’altro, era più bello ed era più facile da installare, perché era posizionato in modo ottimale per il 92 ‘. In seguito, e da quel momento in poi, hanno utilizzato il mio sistema: devi solo progettarlo per bene una volta!
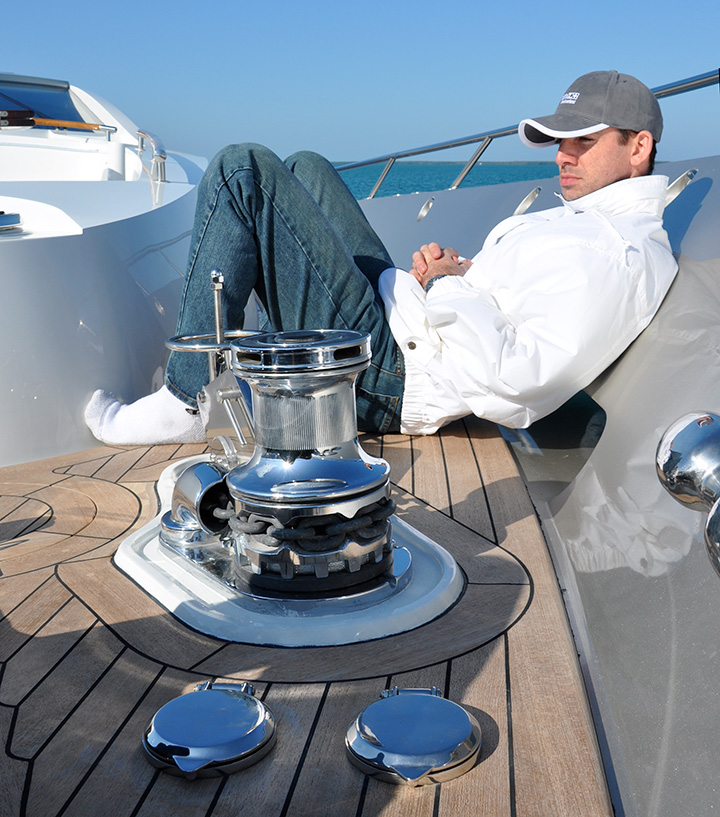
Le scale possono sembrare un ripensamento ma in realtà sono molto complesse. La maggior parte degli yacht compositi sono costruiti con solide scale in fibra di vetro. Invece, ho suggerito di creare una scala “galleggiante”. Consentendo di vedere attraverso le scale e lasciando entrare più luce, lo yacht sembrerebbe più spazioso dall’interno. Hanno apprezzato la mia idea di una scala galleggiante non appena l’ho presentata, e a quel punto ero conosciuto come colui che risolveva ogni problema. È stata sicuramente una sfida per ottenere la forma giusta. L’ergonomia è fondamentale e si destreggia tra l’avere l’impronta più piccola possibile per le scale stesse, ma l’impronta più grande possibile per ogni gradino, un gioco di dare e avere e, cosa più importante ancora: deve essere sicuro. In questo caso la base della scala mobile era anche l’ingresso per il personale, quindi la base doveva essere abbastanza grande da non colpire la testa in caso di onde, e senza perdere troppo spazio.
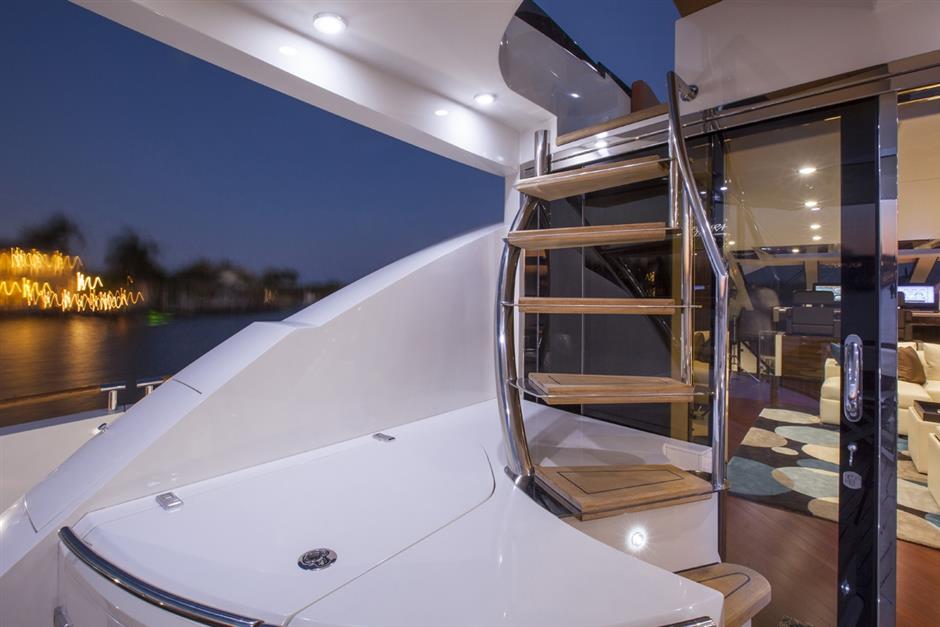
Naturalmente, come per l’intero yacht, il design doveva fluire con il resto della barca e doveva essere a tenuta stagna. Deve essere possibile sigillarlo completamente, se necessario, e tuttavia essere di facile accesso per la maggior parte del tempo. Per questo yacht ho progettato la scala galleggiante esterna e quella dell’equipaggio. Le altre scale sono state aggiornate rispetto al 75′ (23 m) e necessitavano solo di piccole modifiche per corrispondere al 92′ (28 m) . Con misure simili, perché reinventare la ruota?
Di solito lo sportello del carburante si trova nel mezzo di una superficie. L’ho impostato in modo tale che quando si apre la porta laterale per accedere alla barca si ha accesso al tappo del serbatoio del carburante. Innanzitutto, non c’è più un tappo del carburante antiestetico nel mezzo di una superficie, è anche meglio protetto dalle intemperie con meno rischi che l’acqua venga ingerita nel sistema di alimentazione durante il rifornimento e infine meno possibilità di carburante cadendo sul lato della barca.
Sin dal 75′ (23 m), la nostra ditta ha utilizzato i comandi del touchpad per l’illuminazione dell’intero yacht, essendo la prima ditta ad integrarsi completamente con gli yacht. Invece del semplice nome del pulsante, ho incorporato nel pad un disegno grafico di sfondo per abbinarlo al design dello yacht, dando un ulteriore livello di personalizzazione.
Ricordo ancora quando abbiamo presentato lo yacht al salone, e quando la copertura di seta nera a grandezza naturale è stata sollevata, il sussulto udibile del pubblico quando hanno scoperto una coppia che condivideva bicchieri di champagne sul balcone laterale aperto, a solo un metro sopra l’acqua. Il 92′ ha ricevuto molti complimenti e anche premi, e sono orgoglioso di aver fatto parte del team che lo ha progettato.
Questi erano tutti lavori sul prototipo, ma a volte dovevamo anche apportare modifiche per personalizzare una nave particolare. Ad esempio, avevamo realizzato un’altra versione del 92′ che includeva un flybridge più grande in cima, una veranda estesa a poppa, che copriva più dell’area di seduta e anche una piattaforma posteriore estesa.
Uno dei nostri clienti voleva incorporare un tavolo specifico nella sala colazione al piano di sotto. Era un tavolo di vetro spesso circa 4 cm, e di conseguenza metteva a dura prova la posizione della barca che sarebbe stata più scossa se ci fossero state onde forti. Pertanto, ho escogitato una struttura per sostenere il tavolo e, allo stesso tempo, rafforzare il pavimento sottostante. L’altro tavolo di questo cliente era un bellissimo tavolo modulare in vetro Astrolab di Roche Bobois, che includeva una vista su un meccanismo di orologeria. Era fondamentale fissarlo in modo solido e sicuro a terra mantenendo la possibilità di rimuoverlo con facilità se necessario, a lungo termine. Pertanto, ho progettato piedini specifici con dispositivi di fissaggio per tenerlo saldamente e anche garantire l’accesso all’elettricità.
Poi è arrivato il 2009, e ovviamente il mercato del lusso ha sofferto tremendamente, il nostro in particolare con la gamma di yacht medi è stato duramente colpito. La società ha perso diversi contratti esistenti, non c’era altro da fare che mettere il personale in congedo, a parte una squadra ridotta di dieci persone nella ditta (eravamo circa 750 al massimo), me compreso. Avevamo bisogno di trovare dei soluzioni, velocemente. Fino a questo punto la barca più piccola che avevano fatto, che era anche la loro più riuscita, era lunga 68 piedi (21 m). Con l’industria così terribile, abbiamo deciso di creare uno yacht a motore più piccolo nella gamma 64′ che avrebbe avuto un prezzo molto più basso, pur mantenendo il livello di qualità per cui eravamo conosciuti. A questo punto, il capo della ditta aveva piena fiducia in me e mi ha dato libero sfogo, mentre cercava di mantenere a galla l’azienda. Ero il lead designer dell’azienda, quindi ero pienamente responsabile dell’aspetto del 64′.
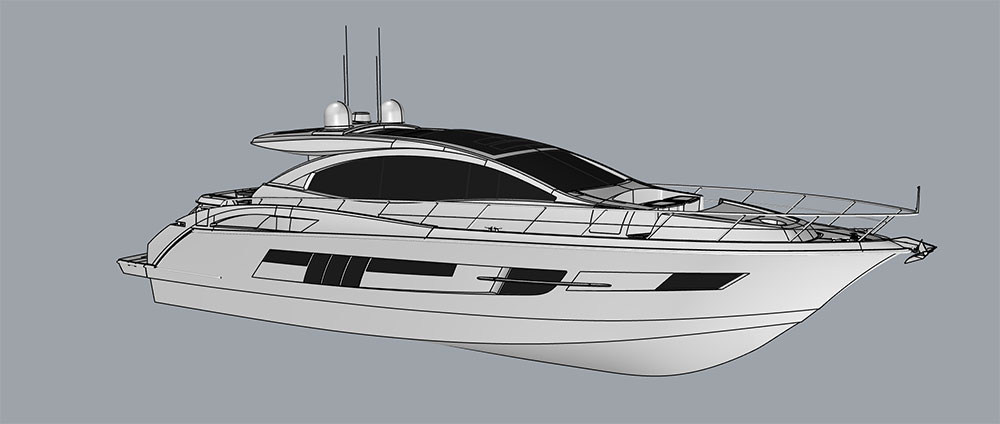
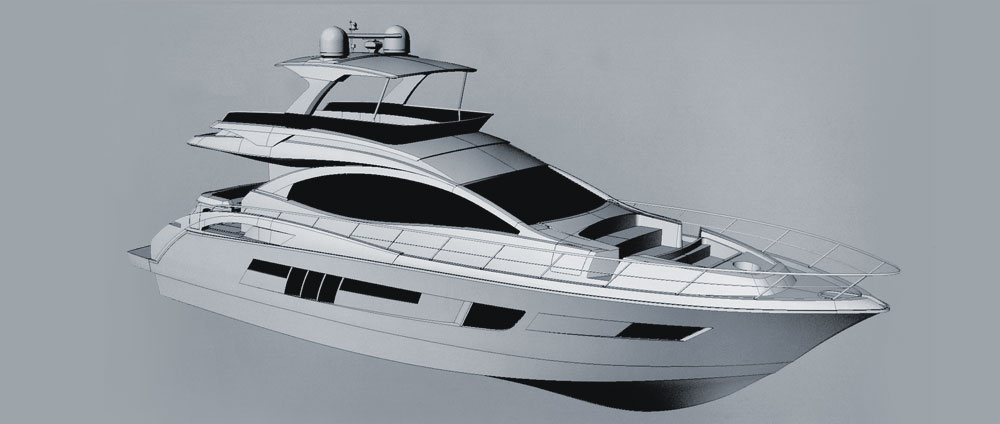
Oltre al solo design industriale, ho fatto del mio meglio per ridurre i costi. Per mantenere la qualità, invece di ordinare cerniere su misura, ad esempio, ho ordinato cerniere standard, ed ho modificato leggermente il nostro design per poterle incorporare perfettamente. Ho anche escogitato un modo per utilizzare lo stesso stampo sia per la versione express che per quella flybridge. Un altro esempio è stato che quando in precedenza abbiamo ordinato un’ancora, abbiamo dovuto farla lucidare; invece ho trovato un’azienda che era uno sportello unico, che ha già fornito un’ancora lucidata e inoltre, ha realizzato il rullo dell’ancora esattamente nella dimensione e nella forma secondo il nostro progetto, con un prezzo un terzo di quello che era prima. Si trattava di come ridurre i tempi e i costi di produzione mantenendo lo stesso livello di qualità, perché eravamo a corto di personale, denaro e scorte.
Più corta è la barca, più difficile è farla sembrare elegante, allungata e spaziosa, e non puoi andare tanto in basso con le altezze del soffitto all’interno per mantenere le proporzioni. Pertanto, per abbassare visivamente il profilo, ho deciso di accentuare l’arco del tetto per mantenere un profilo poco profondo dal lato, pur mantenendo un’altezza del soffitto sufficiente.
Per dargli la sensazione di apertura che volevamo, ho deciso di realizzare un tetto apribile molto grande, in effetti: il più grande possibile. Ho contattato uno dei nostri specialisti del settore e il risultato è stato il tetto apribile più grande mai visto su uno yacht di quelle dimensioni. Mi hanno inviato il file che hanno usato per realizzarlo e l’ho modificato per adattarlo alla nostra estetica e renderlo più facile da costruire. Hanno fatto il meccanismo mentre noi stessi abbiamo realizzato il pannello in fibra di vetro. Il fatto di aver inserito così tanta curvatura nella linea del tetto ha conferito ulteriore rigidità al tetto apribile, motivo per cui ha funzionato. Abbiamo anche aggiunto delle finestre e la loro struttura ha conferito ancora più rigidità al pannello e più luce all’interno.
Ho terminato i progetti di entrambi gli yacht prima di lasciare l’azienda, perché stavo tornando in Europa per motivi personali, ma so che, nonostante il pessimo contesto economico, abbiamo venduto entrambi i prototipi. Purtroppo, la recessione è stata troppo forte e la ditta ha chiuso poco dopo la mia partenza.